Forming Design Style Cabinet
The key points of the design of the forming process for cold-rolled metal steel sheets are as follows:
Material Selection
Material Type
l Choose the appropriate material based on the application, such as low-carbon steel or stainless steel.
Thickness
l Select the appropriate thickness according to design requirements to ensure strength and formability.
Safety Measures
Operational Safety
l Ensure operators follow safety procedures.
Equipment Safety
l Ensure safety devices are functional to prevent accidents.
Forming Process Parameters
Pressure Control
l Adjust the pressure based on material thickness and shape to avoid deformation or cracking.
Speed Control
l Control the forming speed appropriately to ensure quality.
Temperature Control
l Cold-rolled steel sheets are typically formed at room temperature, but heating may be applied if necessary.
Quality Control
Dimensional Accuracy
Strictly control dimensions to ensure they meet design requirements.
Surface Quality
l Inspect the surface to avoid defects such as scratches or cracks.
Equipment Maintenance
Regular Inspection
Perform regular maintenance to ensure proper equipment operation.
Mold Maintenance
l Regularly maintain molds to extend their service life.
Mold Design
Mold Material
l Use wear-resistant and high-hardness materials, such as tool steel.
Mold Structure
l Ensure a reasonable structure to avoid stress concentration and extend mold life.
Environmental Protection and Energy Efficiency
Environmental Protection
l Reduce waste and pollutant emissions.
Energy Efficiency
l Optimize the process to reduce energy consumption.
In
summary
The design of the forming process for cold-rolled metal steel sheets requires comprehensive consideration of factors such as material, mold, process parameters, lubrication, quality control, equipment maintenance, safety, and environmental protection to ensure product quality and production efficiency.
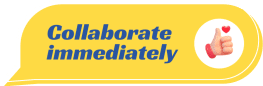